Locked Out: How the Housing Crisis Is Stalling New Construction Projects
Download MP3Even in the face of a housing market decline, inflation, and what people call a housing crisis, there is still difficulty with the pricing of new homes. Builders are having a lot of problems getting homes built for prices that can be accepted by the marketplace. It's not really the fault of the builders trying to mark it up; it's that the supply chain and labor chain are creating enhanced or increased costs of production. What is the solution? Well, a lot of builders are just shutting down, stopping production of speculative homes. If they get a contract from somebody who wants to build a house for custom use, like a homeowner or property owner who just wants to build a specific new house, that's the thing they can do. But even with those contracts, the pricing that comes out in a quote sometimes scares away a buyer.
The cost of materials is still high, even though lumber prices have come down a little bit. The cost of getting workers has gone up. In fact, most builders can't find enough qualified staff to perform the various components of a house: the framing, site work, grading, excavation, and of course, once you get into the skilled trades—electricians, plumbers, HVAC, roofing—sometimes there's just no capacity. In order to get somebody to do that, you have to offer a higher rate to get them to come to your project. The five areas they're talking about are, of course, labor, and that's number one.
One Harvard expert said the solution is to entice more women to join the construction sector and reform immigration law so more immigrants can get construction jobs. Well, maybe those things will work, but that's not going to happen overnight. You can't train a construction worker in a few weeks or months. This is something that, in most cases, requires years of experience. There is about a 650,000 worker shortage on the normal pace to meet demand for this year. Then, next year, they'll need 590,000 on top of that, so that's over a million new workers that are needed. Labor is a bloodbath, according to this one builder. To find anyone willing to work, you've got to pay $30 an hour in some markets. In some of the markets we see in Oregon, Texas, and New York, if you're not paying $40 an hour, you can't get anybody that's any good to work. You might be able to get somebody that shows up for $30, but they're either not going to know what they're doing, they won't show up the next day, or it's just going to be a liability to your job site. At that rate, it doesn't make sense. You have to have people that do more labor-intensive tasks like hauling drywall and moving lumber. If you add that in at $30 an hour, the price of the output home is going to be too high for anybody to want to buy.
Next are the lumber prices. Even though they've come down from their high of about $1,200 to $1,400 for a thousand board feet, it's still above where it was a few years ago. You also have to factor in the fact that they still could go up. If you do a contract today, you have to factor in that lumber could still go up 10% or 20% because it's been volatile. Even if it's at $500 or $600 today, if you don't factor in a lumber price of $700 or $800, you could end up losing money on the job in the long run.
What about lending? That contractor has to have certain money out of pocket up front. Usually, they'll get bridge loans or construction loans, but the higher interest rates are affecting that cost. So, if you're building a house and you have $100,000 or $200,000 out of pocket for six months, that can add a great deal of money—$5,000 or $10,000 worth of additional borrowing costs to your build. That gets passed along in the home price.
What about laws? How does that affect the cost? Well, certainly, the fees are a part of it. Regulations may add $94,000 to the final price of a new single-family home, according to the National Association of Home Builders. It comes in the form of higher impact fees, permit fees, and if the regulations also add time, sometimes that can add more to the price of a house. If, let's say, you could build a house in 90 days under normal conditions, but it takes nine or ten months, those extra six months worth of carrying costs or labor costs can add $30,000 or $40,000 to the price easily. This is because you can't get your house turned out quickly and move on to the next project. All the fixed costs of that builder are still running. The clock is running during that six months: your insurance, your rent for your building that you have your materials in, all your equipment, all of the things that are fixed capital costs for that builder still accrue every month until that house is complete, whether or not they're being used. Those fixed costs are real, and they're things that a lot of builders don't necessarily factor in. That's why they lose money.
Then, there's the cost of land. It's gone up a little bit—not quite as much as the other things—but those go into the ultimate home price. We saw a story about a builder in San Francisco, which is an extreme case. They wanted to build a five-family property in San Francisco. Certainly, if you're going to do that, you have to plan for this in advance. You have to plan years in advance for the permitting, the zoning, and all the other things that go along with it. But if you're a builder and you build one of these every three or four years, maybe you have two that overlap, you can have a nice little career and have something that is your profession. This builder made a point that in San Francisco, it took them 15 years from beginning to end to do this project for this five-unit building. Between waiting for zoning approvals, they had to have all kinds of hearings to get the neighborhood to accept it. Then, once they had the acceptance, they did architectural design, which had to go back three or four times because it was casting a shadow on a schoolyard. There was all kinds of bureaucracy involved. This is in a city that has a housing problem, right? And to get five units built, it took them 15 years.
When they interviewed this builder afterwards, they said, "Look, if I was in any other place, like Texas or Nevada, and I could do this project in a year or two years, I could do 10 of these projects in my lifetime and have a nice little career. Fifteen years each, how many can I do in my life?" If you're a builder who starts as a company at age 35 or 40 and it takes you 15 years to complete a project, you might only do two of them. That adds 30 years to do just two projects. You start at 35 and you're 65 or 70 years old, you may not want to do this anymore.
So, when these projects take a lot of time, you're eliminating getting qualified, expert-skilled contractors to run these projects. You're either going to have somebody who is very young and hasn't done any before, or you get people who are aged out and don't want to do these kinds of projects anymore. So, time can be a bigger factor. It's hidden—it's almost an invisible factor in the building industry. But the more a project takes, the more impact it has on price and even the expertise that goes into it.
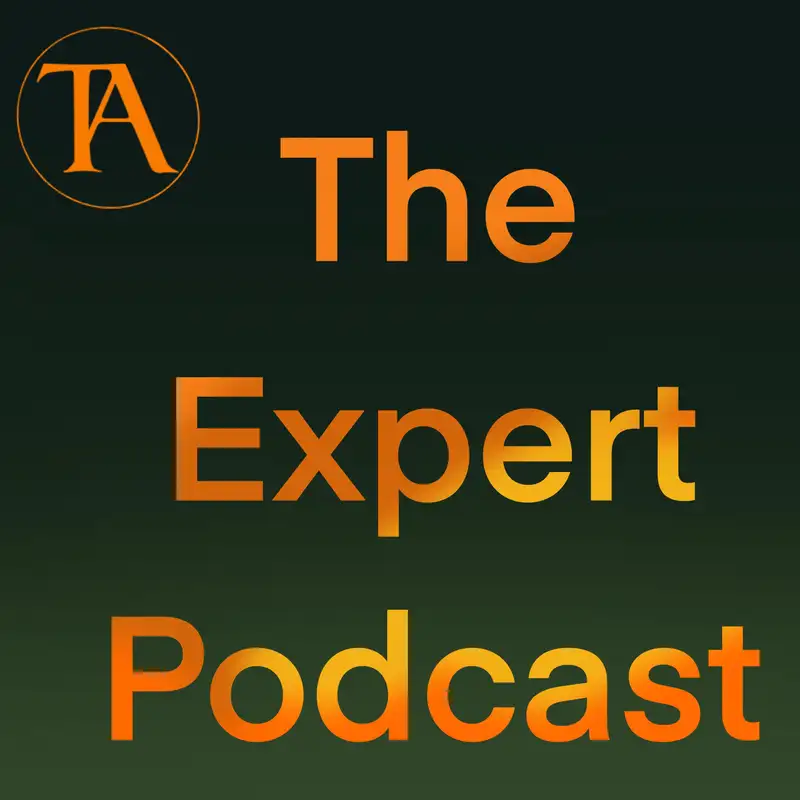