The Calm Before the Storm: Why Construction's Brief Relief Will Give Way to New Delays and Price Spikes
Download MP3# The Calm Before the Storm: Why Construction's Brief Relief Will Give Way to New Delays and Price Spikes
From Maine to Texas to California there are all kinds of things going on with the real estate industry especially construction even in this late spring at the end of May 22. You might think that you're seeing articles about real estate dropping and how is that affecting construction maybe you're waiting for light at the end of the tunnel. The bottom line is inflation for construction is here to stay and even delays are here to stay it's not going to change anytime soon and it comes from every area from lumber materials labor even availability.
There's an article from a local publication local news in Maine that builders are experiencing shortage of labor and materials that's that's really the core of it there's a shortage of labor and materials. You notice he's not talking about the cost of labor or the cost of materials it's a shortage part of it it's delivery truck fuel right.
So let's say you're a builder you're constructing a home and you need all kinds of things. Lumber comes to mind because you see the lumber when you're building a house all you see is lumber first thing you see is the framing of the house the two by fours the sheathing the roofing it's all lumber and then gradually you see paint and other things but when you think about a home being built you think of lumber.
But there's more to it than that most of the materials that go into the house are other than lumber you have the sheetrock you have siding you have roofing you have all your interior fixtures you have a lot of pvc that goes into trim parts plumbing and according to this builder he's been a contractor for 30 years never seen anything like this.
What is he seeing well it's crazy so one of the things he's seeing is that prices are going up by 20 or 30 percent in a short period of time on one day you think that it's going to cost you maybe 15,000 for materials to finish out the inside of a house and then you go to your materials provider and it's gonna cost twenty eight thousand dollars. Well you're just a builder you're passing this along to your client your home owner that's putting on addition or your home buyer that's building the new home so that's going to be a shock.
In addition there might be a delay you might have contracted for a six-month build but now it's going to take nine months that's going to affect the homeowner and you. Well the homeowner now has to have a place to live for at least three months because they probably planned on moving in.
What about you as a builder well you're planning all your jobs out based on completion of this job if you are building this home and took on another job that's going to start in month seven you can't really start that job if you're still involved with this house so now that pushes that one out that throws off your numbers that throws off your revenue for the year because you're not really going to make any more money off of this one house that takes nine months instead of six but now you can't start the next project and start making revenue from that house.
So what do you have to do if you know that projects are going to take longer you have to build more revenue into each project instead of doing three projects a year if you only do two all of your expenses you have to divide up over two instead of divided by three and that's going to affect the pricing on each one especially when the timelines are unknown if you know it's going to take nine months that's one thing but if you don't know might take 10 might take 11 it's harder for you to plan that out you have to leave more gaps in your schedule.
And good builders cost out their variable expenses based on very tight timelines the plumber comes on a certain day electrician the next day sheetrock electrician comes back to do the finished work it's like all in a tight timeline if those are all thrown off now instead of having it be like tetris you know where the blocks fall and you fit them together you have to wait for one block to fall and stop before you even order the next block and that just adds more time in the system.
Any gap of time is time that your equipment is unused while you're making payments on it your employees aren't working while you're paying them your rent electricity all your expenses are still clocks ticking and you're not collecting revenue so it's a bad thing for a builder.
So why is this happening well this station did a great job of interviewing a lumber yard provider. Now what happened was a lot of manufacturers weren't prepared for the surge and they're starting to catch up even things like they need vinyl to make pvc boards you can't get the vinyl so even the factory that makes the pvc trim can't get vinyl to make the trim they also don't have certain colors to make certain color decking things like paint stain very minor things that don't seem like they're a big deal are getting in the way of finishing projects.
In addition that factory that makes the pvc boards they might not have the employees you've heard of the great resignation people are quitting their jobs who wants to work in a pvc plant so those are the first jobs that people quit and even if they didn't quit they might be under quarantine because of covet so they if they have to stay home they can't work.
And now you have an additional problem you have a trucking problem because the fuel prices are up and when fuel prices go up the trucking companies pick and choose their jobs if the shipping is not profitable they're just not going to take the job so it may be that a job that doesn't have as much profit margin to ship that pvc vinyl boards isn't going to make it to the top of the list it might wait three or four weeks or a month until all the other gravy jobs get taken and now they ship those pvc boards that puts a delay where the lumber yard doesn't have the materials to sell.
Even if that delivery is done because of the fuel price and also the higher wages for truckers the the lumber yard has to pay two or three times the cost for delivery for diesel and we didn't even talk about accessories doors windows manufacturers are having trouble getting tempered glass or raw materials for the frames again not enough truck drivers.
In previous years you could get windows in two or three weeks now it's taking longer for anywhere from five weeks to five months so what happens if you're building a house and you want to order windows when do you order them. If you know that from the time that you start framing let's say your site work is done your grading is done you're ready to start pouring your foundation when do you order your windows.
Well if you know your foundation is going to take you know 10 to 14 business days your framing might take 22 business days your dry end might take you know another maybe week or so and okay you're gonna start needing windows in maybe three or four weeks you order them maybe when you start framing or maybe when you're your foundation's done.
Well now if it's going to take five months you need to order them before you start doing foundation but what if they show up early you got to store them you got to make sure they're not getting damaged you got to pay for them early so it throws all the efficiency of organization off at the same time if you don't have enough windows now your employees are sitting around.
Here's what he says there are many times when there's only enough windows for one job and now you have all your employees sitting around doing nothing because you don't have other jobs for them to work on so all these things may seem small by themselves but they add up to create big problems for the builder for the client for the property owner and even for insurers.
Now with the real estate market seemingly cooling off meaning less people are buying homes there are some places that the building permits are going down meaning that builders are filing for less permits well let's take a look at that why might that be happening.
Think about what we just discussed with materials and lumber and labor if you're a builder and you know for a fact it's going to take you five weeks to get windows and the materials prices might be 30 more are you going to bother trying to build a house that you don't know is going to sell for a certain amount or are you going to apply or you're going to take on a contract for a remodel if you don't know if you're going to be able to get parts.
Look if you do a contract with a client for a remodel for a certain price let's say it's going to be a 1500 square foot addition on a house and you know your contract for that is you know two hundred and sixty thousand dollars you gotta pull permits and you're gonna start that process.
Well now that you know that the materials prices might go up maybe the delays might come into play so instead of pricing at 260 you're going to price it at 320 give yourself some leeway and also instead of saying a six month turnaround you're going to say a nine month turnaround well you may have fewer clients take that deal because it might be out of their budget might be out of their timeline so there's less permits.
Now what happens when there's fewer homes being built or additions being built well now it's like a spiral because now the builder has less projects to work on so they have to price the ones they do have higher to cover their fixed expense the backlog of homes for new home buyers goes down so the resale market goes up right you see how that spiral works.
So if you're a builder you may not be as ambitious or aggressive about projects in fact it's making the labor pool even more dire because as builders do less projects they have less work for skilled trades people framers plumbers construction people roofers so when there's less work for those individual trades they're going to go do something else they're going to get into another line of business maybe they'll they'll go work on the the shrimp boat and maybe they'll go move to another state where there's work and now it's a deepening spiral so now you have to pay more for that labor in your home market.
This is all adding up for contractors and it's affecting consumers as well because the home market is taking a little bit of a pause so people are backing off from buying because the prices are up but they're still the same number of people who need a home the people who need homes didn't go away it's just the price went up.
So as it takes a pause builders who are filling that market back filling the housing units are not going to be that ambitious and aggressive about doing it if they see people like putting the brakes on buying houses which is going to mean that there's fewer houses being built and that could lead to a su even more severe housing crisis in years to come.
Let us know what you think in the comments see in the next video.
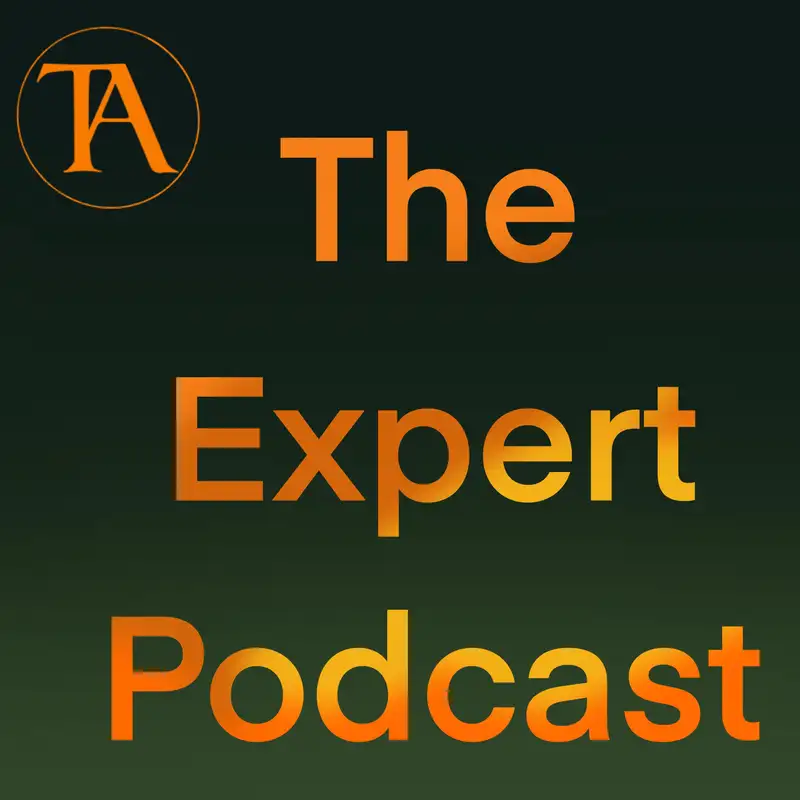